Alright before I get started on this idea I assume that I will get remarks about this idea being "rice" but i think it would be a interesting project.
The idea that i have is to make carbon fiber intercooler pipes or piping.
My idea for the first piece is to go from the throttle body and eliminate the 3000 pipe and have it extend to where the pipes go into the fender. As such but without the couplers:
(hope Supra8795 doesn't mind me using the picture)
The problems that I see with this project are:
And here are what I have researched and came up with for solutions:
1. For making the mold I was just going to get a piece of metal mandrel bent to the shape that I desired.
2. Now this is tricky because normal epoxy's loose there structural strength usually over 250F degrees and start to discolor. Well I have found a relatively cheap epoxy that can handle and up to 400F degree temperatures and actually become stronger as it is heated because it cures the epoxy more.
Epoxy
3. Now this was the hardest part to over come that I could see. Most pipes or tubes that are made are made from a 2 part mold and then put together using an adhesive. Well I have a hard time with this idea because it just has accident written all over it, I mean this has to with stand a good amount of pressure and I dont want it to fail.
So as a result I have found a SITE that sells carbon fiber sleeves that are similar to this.
Now the site sells various diameter sleeves and different weights at a very reasonable price. Im looking at using the 2.5'' sleeve.
Procedure:
My idea is to get a pipe bent to the desired shape and length, Next you prepare the pipe by putting down a wax so that the epoxy will not stick to the pipe. After that is done you take 2-3 sleeves and put it around the pipe. After those are on there you apply the epoxy resin. Now heres the niffty part, the site that sells the sleeves also sells shrink wrap that is resin resistant. So when you have the carbon fiber wet with resin you then take the shrink wrap and place it over it. By heating it, it presses the excess resin out and applies a nice smooth finish similar vacuum bagging.
So what do you guys think? I want to hear your guy's thoughts about the idea and if you think there is anything that I am missing?
Thought it would be nice because it is carbon fiber and it has the properties to not conduct heat as well as metal.
The idea that i have is to make carbon fiber intercooler pipes or piping.
My idea for the first piece is to go from the throttle body and eliminate the 3000 pipe and have it extend to where the pipes go into the fender. As such but without the couplers:
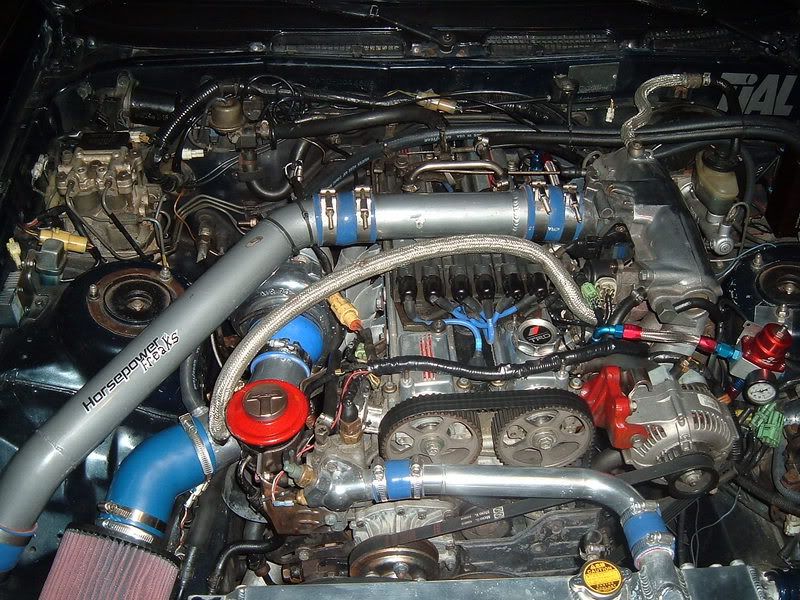
(hope Supra8795 doesn't mind me using the picture)
The problems that I see with this project are:
- How to make the mold
- The temperatures within the hood ruining the epoxy
- Having the pipe be seamless so there is no chance of splitting under pressure
And here are what I have researched and came up with for solutions:
1. For making the mold I was just going to get a piece of metal mandrel bent to the shape that I desired.
2. Now this is tricky because normal epoxy's loose there structural strength usually over 250F degrees and start to discolor. Well I have found a relatively cheap epoxy that can handle and up to 400F degree temperatures and actually become stronger as it is heated because it cures the epoxy more.
Epoxy
3. Now this was the hardest part to over come that I could see. Most pipes or tubes that are made are made from a 2 part mold and then put together using an adhesive. Well I have a hard time with this idea because it just has accident written all over it, I mean this has to with stand a good amount of pressure and I dont want it to fail.
So as a result I have found a SITE that sells carbon fiber sleeves that are similar to this.

Now the site sells various diameter sleeves and different weights at a very reasonable price. Im looking at using the 2.5'' sleeve.
Procedure:
My idea is to get a pipe bent to the desired shape and length, Next you prepare the pipe by putting down a wax so that the epoxy will not stick to the pipe. After that is done you take 2-3 sleeves and put it around the pipe. After those are on there you apply the epoxy resin. Now heres the niffty part, the site that sells the sleeves also sells shrink wrap that is resin resistant. So when you have the carbon fiber wet with resin you then take the shrink wrap and place it over it. By heating it, it presses the excess resin out and applies a nice smooth finish similar vacuum bagging.
So what do you guys think? I want to hear your guy's thoughts about the idea and if you think there is anything that I am missing?
Thought it would be nice because it is carbon fiber and it has the properties to not conduct heat as well as metal.