i wanted to post this thread for a few reasons. I have an upper end knock, caused by too much wear in the cams, even though my lifter shims are very close to being within specs, it still knocks a lot.
i grabbed a set of good cams from the junkyard (n/a motor) and here is what they looked like:
notice the normal wear on the babbit material that usually scares most people. you can definitely tell that it is a soft material, and if you can feel grooves in the metal, the cam is bad.
i took the cams to my machinist and had him micropolish the journals. i then removed the oil coking from the lobes with a die-grinder with a scotch brite pad attatchment.
results:
as you can see, the cams were fine, before and after, all journals measure within spec according to the tsrm.
as a second note, when i took apart my top end, i discovered what had been causing the knock, and the oil leak that i had at the front of the block.
this wear was caused by the previous cams being scored (really scored, not just the babbit coating). i had re-used these cams and over tightened the timing belt. note: timing belt tension is automatically set by the spring on the tensioner. i had pried the tensioner pulley to tighten the belt and then tightened it. oops.
all in all, now the head needs to be replaced, so don't let this happen to you. the cams and cam journals in the head are often overlooked, but are very important.
i grabbed a set of good cams from the junkyard (n/a motor) and here is what they looked like:
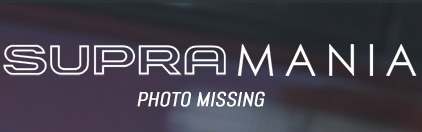

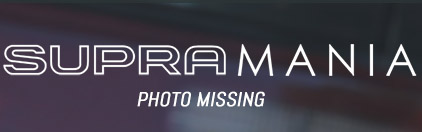
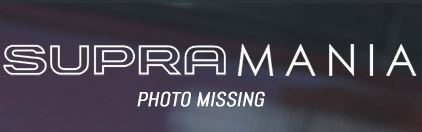
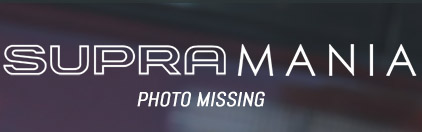
notice the normal wear on the babbit material that usually scares most people. you can definitely tell that it is a soft material, and if you can feel grooves in the metal, the cam is bad.
i took the cams to my machinist and had him micropolish the journals. i then removed the oil coking from the lobes with a die-grinder with a scotch brite pad attatchment.
results:
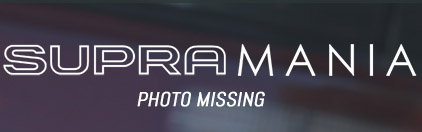
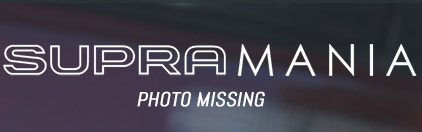
as you can see, the cams were fine, before and after, all journals measure within spec according to the tsrm.
as a second note, when i took apart my top end, i discovered what had been causing the knock, and the oil leak that i had at the front of the block.
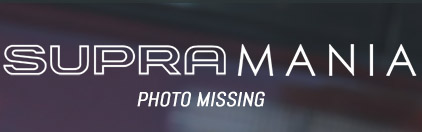
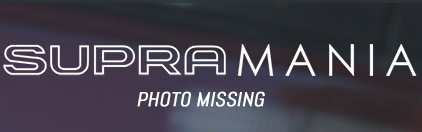
this wear was caused by the previous cams being scored (really scored, not just the babbit coating). i had re-used these cams and over tightened the timing belt. note: timing belt tension is automatically set by the spring on the tensioner. i had pried the tensioner pulley to tighten the belt and then tightened it. oops.
all in all, now the head needs to be replaced, so don't let this happen to you. the cams and cam journals in the head are often overlooked, but are very important.