Thought I'd share my current project with a few pics since I have had some people ask. I am currently in the process of rebuilding my old cnc mill (gantry style) and a new mini mill.
The mini mill is made from the guts of a dentistry mill I recently got at an auction ($40) and was rated down to a 3 micron accuracy. Judging by the quality of the parts inside this thing I don't doubt that.
The plan is to have it hook up to my current controller and driver electronics which are also created from scratch from parts I salvaged from an old photocopier.
The 2nd machine is in it's 5th revision now and started it's life originally as 3 old photocopiers. Itwas capable of cutting 1/4" aluminium sheet fairly nicely but I wanted to improve it's performance (speed) and make it more accurate and also increase it's cutting area.
The first pics are from the XY table of the new mini mill, which will be a standard column and table mill layout when finished. It has a relatively small cutting area but should benefit a lot from the quality of parts and spindle from the donor machine.
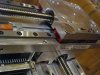
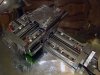
And this is just a pic of the new rails that I am upgrading the old machine with I just got. I'll snap some pics of the old machine today and update later.
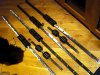
Here's a little side thing I made yesterday before breakfast. Still working on it, far from done, but shows the flexibility of my machine to be able to cut aluminum and vinyl.
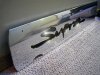
The mini mill is made from the guts of a dentistry mill I recently got at an auction ($40) and was rated down to a 3 micron accuracy. Judging by the quality of the parts inside this thing I don't doubt that.
The plan is to have it hook up to my current controller and driver electronics which are also created from scratch from parts I salvaged from an old photocopier.
The 2nd machine is in it's 5th revision now and started it's life originally as 3 old photocopiers. Itwas capable of cutting 1/4" aluminium sheet fairly nicely but I wanted to improve it's performance (speed) and make it more accurate and also increase it's cutting area.
The first pics are from the XY table of the new mini mill, which will be a standard column and table mill layout when finished. It has a relatively small cutting area but should benefit a lot from the quality of parts and spindle from the donor machine.
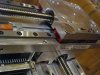
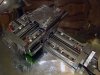
And this is just a pic of the new rails that I am upgrading the old machine with I just got. I'll snap some pics of the old machine today and update later.
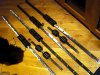
Here's a little side thing I made yesterday before breakfast. Still working on it, far from done, but shows the flexibility of my machine to be able to cut aluminum and vinyl.
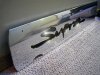